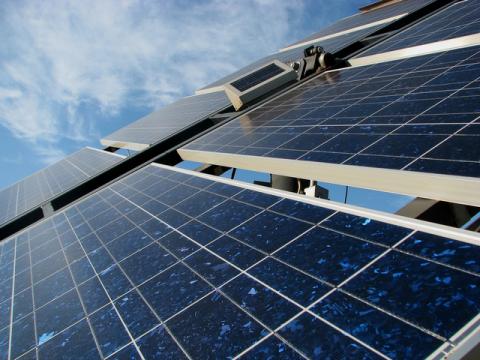
For the past few weeks we shined the spotlight on the Semiconductor Application; we've looked at WHAT happens in a facility and WHY monitoring is necessary in the different parts of the facilities (PPM, LFL, and Area). This week let's discuss HOW, by looking at real life application:
Solar Panels Case History
A worldwide manufacturer of solar electricity panels uses a multiple zone, conventional printing dryer. A special foil substrate is passed through rollers that transfer a proprietary ink formulation and epoxy adhesive coating to the film surface. The ink contains mixtures of muliple solvents. After the ink has been applied to the foil, it is run through a dryer to evaporate off the solvents.
The Company needed to purchase LFL analyzers to monitor the atmosphere in their dryer. They needed an industrial strength analyzer that could handle multiple solvents, water vapor and most importantly epoxy based adhesives. They required an analyzer that when calibrated would remain accurate for all constituents in the sample.
They chose the PrevEx flame temperature technology over Catalytic and Infrared due to its ability to handle the tough sample environment. The constituents of the sample could coat or corrode a catalytic sensor and foul the optics of the IR, resulting in false or unreliable readings. In addition to its rugged industrial design, fast response and operating simplicity, the PrevEx analyzer is free from poisoning by resins, plasticizers and silicones. It gives consistent and reliable readings with multiple solvent concentrations and runs at a temperature high enough to keep all the dryer atmosphere elements in the vapor state.
- Each zone on the dryer required monitoring to measure the flammable concentration and detect build-up of any solvent vapors, so the analyzers are mounted directly to the process ductwork for the best representative sample.
Find out more details.
Add new comment