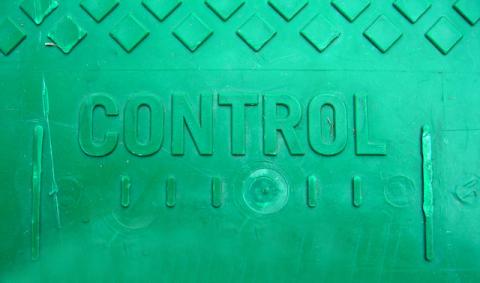
Variable ventilation controls allow the maximum reduction in ventilation, and thus maximum economy. It also allows some extra corrective action but also one important safety concern: Variable ventilation is based upon the measurement of the L.F.L. concentration and adjustment to ventilation rates through damper or blower controls.
There are two main types:
- two-level
- feedback
The two-level control has settings for the maximum ventilation and for reduced ventilation, and switches between these two ventilation rates using the "warning" high-limit alarm of the analyzer or some similar scheme.
The feedback control has a range of continuous ventilation adjustment which uses a feedback loop to control the L.F.L. concentration to a particular set-point.
When variable ventilation is used, safety is improved because the ability to increase the ventilation rate to a very high level performs a very powerful corrective action in the case of a sudden increase in solvent load. However, because the analyzer is part of the feedback loop, it is a control device rather than safety device. Analyzer failure, in particular an undetected loss of sensitivity, can automatically cause a false low ventilation rate. In effect, this can multiply the LFL concentration proportionally to the percentage loss of analyzer reading.
If the control point is 50% LFL, then an undetected loss of 50% analyzer sensitivity poses a serious risk of exceeding the LFL and causing a fire or explosion. For this reason, catalytic sensors, or other sensor types which by their nature will loose sensitivity over time and from exposure to catalytic poisons, and require frequent increases to signal amplification (span), are generally unacceptable for variable ventilation controls.
The problem of analyzer failure in a control loop has two potential solutions, both recognized by NFPA-86:
- addition of a second analyzer to perform the safety function
- maintenance of minimum ventilation for worst-case 50% LFL (or another appropriate upper limit)
Since the analyzer is part of a control loop, the important criteria for stability include the analyzer response time, the dryer response time, and the response time of the corrective action such as dampers. The dryer response time varies from as little as a few seconds to as high as one minute or more. The analyzer response time ("time to alarm") should always be less than the dryer response time. The time for corrective action, when combined with the analyzer response time, should be less than the time for the dryer to reach a dangerous condition: this is less than two times the dryer response time, or whenever possible, less. Therefore fast-opening pneumatic dampers with spring returns and positioners are preferable to slow electric dampers. The latter might take 30 seconds or more to open fully, which is a very long time compared to the typical dryer response time.
The dampers should open as quickly as possible (ventilation increase to maximum), at the "warning" high limit alarm, when the speed accelerates (feed-forward), and during start-up of the heaters or the conveyor. They should close very slowly: on the average a 30 second time for closing the dampers is preferable. Regular testing of the damper functions is essential - they are as important as the analyzer in the method of control. Because of the special conditions, implementing closed-loop control requires special control algorithms.
Maximum ventilation should also be used whenever the analyzer is undergoing any type of calibration or maintenance procedure while operating. The potential to inject "zero" gas to the sensor when in fact the process ventilation is being controlled to 50% L.F.L. illustrate the great importance of proper security and interlocks on calibration controls.
Add new comment