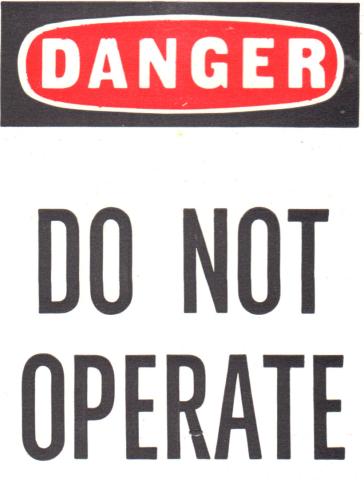
The conversation around Safety Integrity Level (SIL) has picked up among the industrial community; but what exactly is everyone saying and how does it apply to YOUR process?
Let’s attempt to break down this often-misunderstood concept and learn how it can be implemented properly. To fully understand a complex concept like SIL, there are a few other aspects to consider, this week we’ll focus on functional safety.
FUNCTIONAL SAFETY
The International Electrotechnical Commission (IEC) defines functional safety in the 61508 standard as “the detection of a potentially dangerous condition resulting in the activation of a protective or corrective device or mechanism to prevent hazardous events arising or providing mitigation to reduce the consequence of the hazardous event.”
This concept is a pivotal part of the overall safety of a process, ensuring a system or equipment is operating appropriately and actively preventing the failure of a system from causing harm to people and property. Exida, a certifying agency for functional safety, states, “the goal of functional safety is to design an automatic safety function that will perform the intended function correctly or the system will fail in a predictable (safe) manner.”
Functional Safety was developed as the need for more confidence in safety systems arose around the world, due to major accidents and increasing reliance on electronic programmable systems to carry out safety functions. Agencies and industry experts felt the need to develop standards focusing on reducing the risk level in the process. Safety systems needed to be designed to prevent dangerous failures AND control them should they arise.
- An example of implementing a functional safety system would be enabling a shutdown of the processing units when a nonstandard situation occurs that the regulatory control system or operators can not correct, in order to prevent a catastrophe.
Add new comment