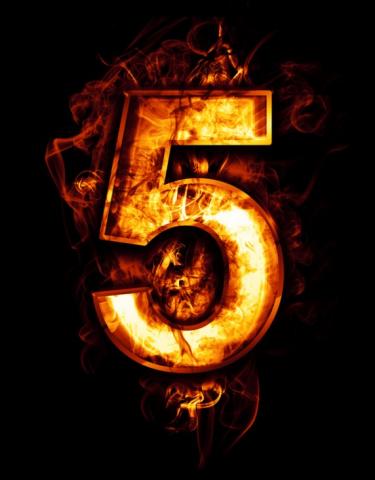
For the past few weeks we've talked about the problems that plague the coil coating application, including: maintenance, sensor accuracy, and response time. However, there is a solution to all three.
Because of its unique construction and operating technology our PrevEx Flammability Analyzers are the optimum solvent vapor analyzers for coil coating atmospheres, for five key reasons:
1. Excellent in High Temperature Processes
- operating temperature is high enough to keep all oven atmosphere elements in the vapor state
- avoids condensation & maintenance problems through its simple flow system, which has no capillaries that can clog or pumps that can fail
- mounts directly on the oven wall or exhaust duct without external sample lines
2. Efficient Operation Reduces Maintenance
- complete stand-alone LFL system, that’s easily operated and maintained
- predictive maintenance, a “service needed” message and relay contact, which anticipates the need for maintenance before faults occur
- efficient operation, like the avoidance of sample condensation, reduces service to routine maintenance
3. Fastest Response Time
- By mounting directly on the process duct without heat trace sample lines, pumps, or blowers, sample path is significantly shortened
- sample delivery time is an industry best, 1-second response time
4. Universal Calibration
- gives close - to - linear response for a wide range of solvents without recalibration or correction when solvents are changed (this feature is particularly efficient in coil coating where solvent mixtures can change as different products are manufactured)
5. Fail Safe Operation
- Inherent design of the sensing flame technology is that the flame must always be on and the system working properly or an alarm is given
- Whether it is a loss of fuel, air, sample flow or power, a malfunction relay is automatically tripped and the operator is notified immediately of a status change
Add new comment